自動組立カシメ装置によるリレー製造ラインの無人化
こちらは、複数の端子部品を用いたリレー製造ラインを、自動組立カシメ装置を導入することでライン全体の無人化を行ったプロセス改善事例です。
ここがポイント!
- タクトタイム3秒でも自動組立に対応!
- 困難な位置出しとカシメも高精度に対応!
- リレー製造ラインの無人化を実現!
Before
- 部品の整列
- 端子部の組付け
- カシメ
- 目視検査
- 搬送
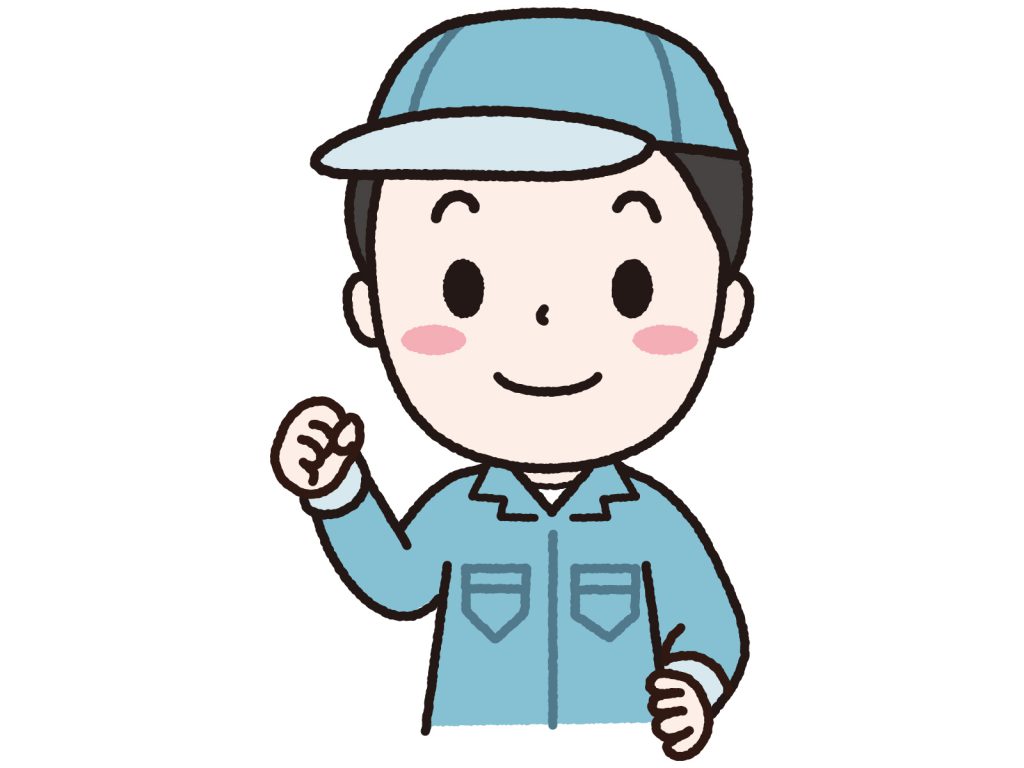
改善前は、作業者数人がかりでリレーの端子部の加工から組立、カシメ後の品質検査までを行っていました。
このリレー部品は約10mmという小型部品であり、かつ5種類以上の端子部品を組付ける必要があったため、丁寧な組付け作業が必要でした。しかし、作業者による手作業であるため、不良品率を低減できない状況でした。また、小さい部品の目視検査でも不良品を見落としてしまう可能性がありました。
そこで、ライン全体での品質向上と高効率化を図るべく、ラインの無人化をお客様と一緒に検討いたしました。
After
- 部品の供給
- 搬送
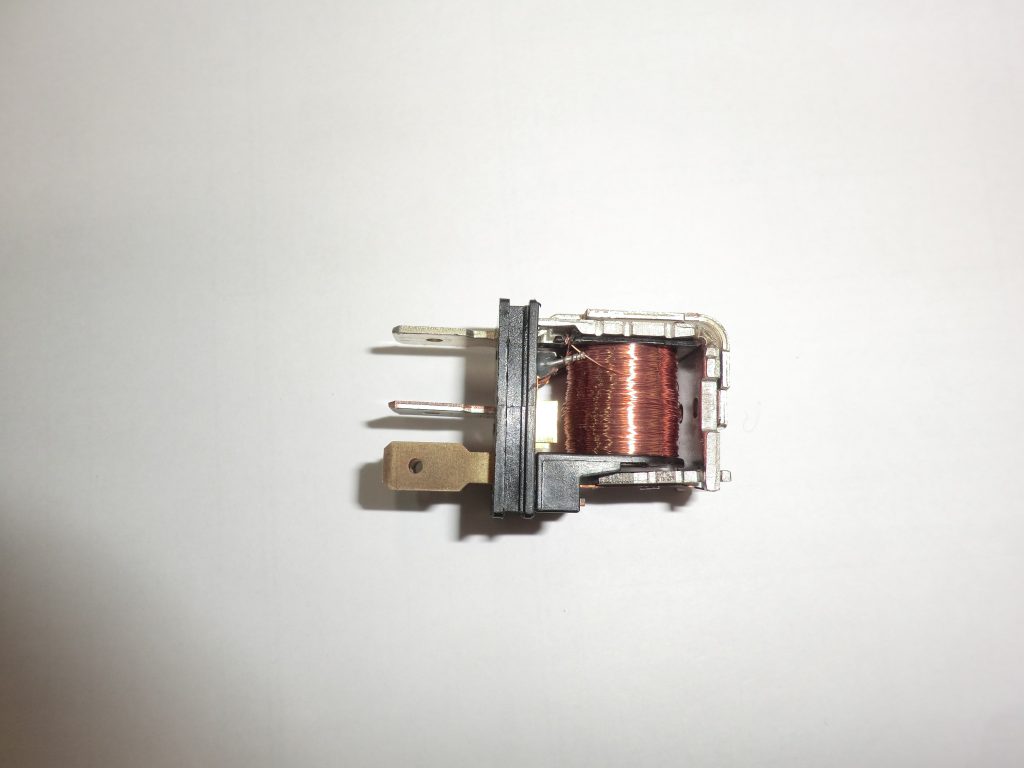
そこで工場無人化ナビでは、自動組立カシメ装置を導入して全長18mのラインを無人化することを提案いたしました。
まず、フープ材から供給される端子部品を30tプレス装置で切断・曲げ加工します。そして、樹脂のボディをベースに、抵抗やリレー端子等の5種類の部品を自動で組付け・カシメを行い、サブコンベアによって本ラインまで搬送・投入します。このリレー製造では2個ずつ同時に組み立てを行うため、位置出しの難易度が非常に高い製造ラインでした。また、タクトタイムが3秒と短いためカムP&Pを使用していますが、樹脂ボディに対して圧入によって端子部品を組付けるため、P&Pヘッドにシリンダを追加することで短いタクトタイムにも対応できるようにしました。さらに、カシメ形状を同一形状にすることが困難だったため、メカの調整を何度も行うことで、お客様のご要望基準を満たすように仕上げました。
この自動組立カシメ装置を導入することで、、作業者が全く関与せずに精度の高い組付工程を行うことができるようになりました。また、自動画像検査によって不良品の発生も抑えることができるようになりました。
結果として、リレー製造ラインの品質安定化と同時に無人化を実現することができました。